GRP Filter: A Key Technology for Water and Wastewater Treatment
In the field of water treatment, the (Glass Reinforced Plastic) GRP filter has become a prominent choice due to its durability, corrosion resistance, and efficiency. These filters are used in a wide variety of applications, from municipal water treatment to industrial wastewater management. But what exactly is a GRP filter, and how does it work? Let’s dive deeper into this innovative filtration technology and explore its benefits.
What Is a GRP Filter?
GRP filter is a type of filtration system made from glass-reinforced plastic, a composite material that combines fiberglass with resin. This material is lightweight, yet exceptionally strong and resistant to corrosion, making it ideal for applications that involve exposure to harsh chemicals, extreme weather conditions, or high pressures. The unique properties of GRP make these filters a preferred option in water treatment systems where longevity and resistance to chemical damage are essential.
How Does a GRP Filter Works?
GRP filter functions similarly to other types of filters, using physical mechanisms like mechanical filtration and adsorption to remove impurities from water or wastewater. Water is passed through a bed of filter media, such as sand, gravel, or activated carbon, which traps particles and contaminants.
GRP filter often comes in two configurations:
- Pressure Filters: GRP Cartridge Filter: These are pressurized systems, where water flows through the filter under pressure, forcing it through the cartridge filter element i.e: String Wound, Melt-Blown or Pleated Filter Cartridge.
- Gravity Filters: These rely on the natural force of gravity to pull water through the filter media – particularly: sand, gravel and anthracite and in smaller systems GAC (Granular Activated Carbon, GreenSand and Ion Exchange Resins) – making them suitable for removing particles of a certain micron size (up to 50 microns) and also Chlorine, Hardness (Ca + Mg) and Iron.
The filtration process can remove a wide range of contaminants, including:
- Suspended solids (e.g., dirt, sand, and silt)
- Organic matter (e.g., algae or bacteria)
- Chemicals and heavy metals (e.g., iron, chlorine, and fluoride)
Key Benefits of GRP Filters
-
Corrosion Resistance: One of the primary advantages of GRP filters is their resistance to corrosion. Unlike metal filters that can degrade over time when exposed to water and chemicals, GRP filters remain unaffected by rust, making them ideal for use in coastal or chemical-intensive environments.
-
Lightweight and Easy to Install: GRP filters are significantly lighter than metal or concrete alternatives, which makes them easier and more cost-effective to transport and install. This feature is particularly valuable in areas where infrastructure costs need to be minimized.
-
Durability: The glass-reinforced plastic construction offers exceptional strength, allowing GRP filters to withstand high pressures and temperatures. This durability translates into a long lifespan, reducing the need for frequent replacements and maintenance.
-
Cost-Effective: Although a GRP filter may have a higher upfront cost compared to some other materials, its long-term performance, low maintenance needs, and resistance to wear and tear makes it a cost-effective option in the long run.
-
Customizable: A GRP filter can be manufactured in a range of sizes and configurations, making it suitable for small-scale residential applications as well as large industrial and municipal systems.
Applications of a GRP Filter
GRP filter is versatile and find application in numerous industries and systems. Some of the most common uses include:
-
Municipal Water Treatment: A GRP filter are widely used in municipal water treatment plants to purify drinking water. It is ideal for removing particulate matter, microorganisms, and other contaminants from water before it reaches consumers.
-
Industrial Wastewater Treatment: In industries such as food processing, pharmaceuticals, and textiles, a GRP filter helps treat wastewater by removing suspended solids and chemicals, ensuring that the water meets environmental discharge standards.
-
Aquaculture: GRP filter is used in fish farms and other aquaculture applications to ensure that the water quality remains high by removing debris and maintaining a clean environment for aquatic life.
-
Swimming Pools: GRP filters are often found in swimming pool filtration systems, where it helps to remove fine particles and bacteria, ensuring that pool water remains safe and clean.
Maintenance and Considerations
While a GRP filter is relatively low-maintenance, it requires periodic cleaning and monitoring to ensure optimal performance. The filter media or cartridge filter elements may need to be replaced over time, depending on the type of contaminants being filtered and the volume of water being treated. Regular inspections of the GRP filter housing and pressure gauges are essential to identify any potential issues.
Additionally, it’s important to consider the quality of the incoming water, as very high levels of certain contaminants (e.g., iron or manganese) may require additional treatment steps, such as pre-filtration or chemical dosing, to optimize the performance of the GRP filter.
Conclusion
GRP filter offers a reliable, efficient, and cost-effective solution for water and wastewater filtration. With its corrosion resistance, durability, and ease of installation, it is an excellent choice for a wide range of applications, from municipal water treatment to industrial wastewater management. As water quality continues to be a priority in both residential and commercial sectors, the use of GRP filters will likely increase, ensuring cleaner water for people, industries, and the environment.
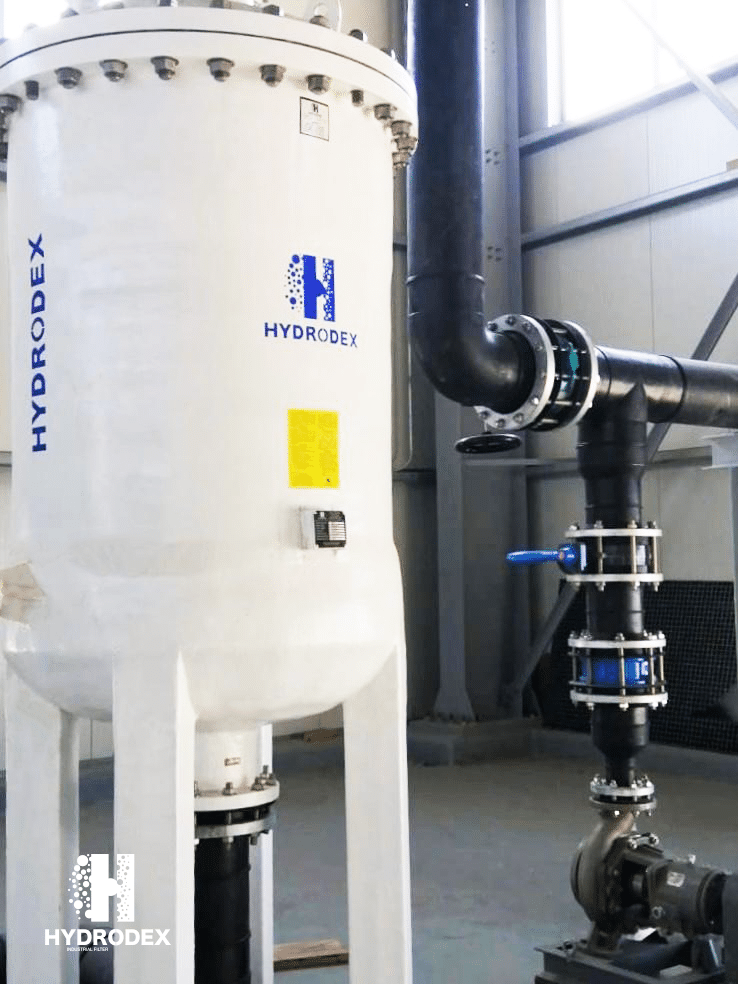
Hydrodex GRP Filter Housing
In the world of water treatment systems, ensuring the integrity and reliability of filtration components is paramount. One essential part of these systems is the (Fiberglass Reinforced Plastic) FRP filter housing. Known for its durability and strength, the FRP filter housing is becoming increasingly popular in a wide range of industries for its superior performance. In this article, we will explore what FRP filter housing is, its technical specifications, and the advantages it offers in water treatment systems and specially seawater desalination systems.
What is FRP Filter Housing?
FRP filter housing is a type of filtration system component designed to hold filter cartridges and ensure efficient filtration of water or other liquids. Made from a combination of fiberglass and resin, these housings offer an ideal solution for many industries, including water treatment, chemical processing, food and beverage, and pharmaceuticals.
The FRP filter housing is built to withstand the pressures, chemical exposure, and demanding conditions found in industrial applications. Its ability to handle high pressure, combined with resistance to corrosion, makes it a preferred choice for systems requiring long-term durability and performance.
Technical Specifications of FRP Filter Housing
-
Material Composition
The housing is constructed using fiberglass wound around a resin core, creating a lightweight yet highly durable product. The fiberglass provides strength and resistance to corrosion, while the resin offers flexibility and bonding properties. This combination gives FRP filter housing its robust structure and resistance to harsh environmental conditions. -
Pressure Rating
FRP cartridge filter housing is designed to handle high pressures, typically up to 150 psi or more. This makes it suitable for both low and high-pressure water filtration systems. The pressure rating ensures that the housing can maintain its integrity under a range of operational conditions. -
Temperature Range
The FRP filter housing can operate within a temperature range from 40°F to 150°F (4°C to 65°C). This temperature tolerance allows it to be used in various environments, whether they involve warm water or other fluid media. -
Corrosion Resistance
One of the main advantages of FRP filter housing is its ability to resist corrosion. Unlike metal housings that can rust or degrade over time when exposed to water, chemicals, or extreme weather, FRP housing offers a superior level of protection against corrosion. This extends the lifespan of the housing and reduces maintenance costs. -
Capacity and Size
FRP cartridge filter housings come in various sizes and configurations, depending on the specific needs of the filtration system. They can accommodate a wide range of filter cartridges, from standard sizes like 10″, 20″, 30″, 40″, 50″, 60″ and 70″ to customized dimensions based on flow requirements. -
Filtration Efficiency
The efficiency of the FRP cartridge filter housing depends on the type and micron rating of the filter cartridges used. The housing ensures that these cartridges are securely placed, preventing any bypass of unfiltered water. This is crucial in applications where high filtration standards are required, such as in pharmaceuticals or food processing.
Benefits of Using FRP Filter Housing
-
Enhanced Durability
The combination of fiberglass and resin gives FRP filter housing exceptional durability. This ensures long-term reliability even in harsh conditions, such as exposure to chemicals, UV light, and extreme temperatures. -
Cost-Effective Solution
While FRP filter housing is highly durable, it is also cost-effective compared to other materials like stainless steel. The lower material costs, combined with reduced maintenance requirements due to its corrosion resistance, make it an economical option for businesses looking to maintain high filtration performance without breaking the budget. -
Lightweight Design
Compared to metal alternatives, FRP cartridge filter housings are lighter and easier to handle during installation. This reduces labor costs and makes installation more efficient, especially for larger systems. -
Customizable to Meet Specific Needs
FRP filter housing can be customized in terms of size, configuration, and pressure ratings to meet the unique demands of various filtration applications. This flexibility allows businesses to design systems that are tailored to their specific requirements. -
Environmentally Friendly
As fiberglass is a lightweight and strong material, FRP filter housing can contribute to a reduction in the carbon footprint of filtration systems. It also reduces the need for frequent replacements compared to materials that wear out faster.
Applications of FRP Cartridge Filter Housing
-
Water Treatment: FRP filter housings are commonly used in both industrial and residential water treatment systems. They effectively remove suspended particles, chlorine, and other contaminants from water, ensuring clean, purified water.
-
Chemical Processing: In industries where corrosive chemicals are used, FRP filter housing offers a reliable solution for filtration without the risk of degradation over time.
-
Food and Beverage Industry: Ensuring clean water and the filtration of liquids is crucial in food processing. FRP cartridge filter housing is used to guarantee that the end product is free from contaminants.
-
Pharmaceuticals: The pharmaceutical industry demands the highest standards of filtration to avoid contamination. FRP filter housing ensures that filtration systems are reliable and meet stringent safety standards.
Conclusion
FRP cartridge filter housing is a vital component in modern filtration systems due to its durability, cost-effectiveness, and adaptability. Whether in water treatment, chemical processing, or food production, FRP filter housing delivers unmatched performance, handling high pressures and offering superior corrosion resistance. By investing in FRP filter housing, businesses can ensure that their filtration systems remain reliable, efficient, and cost-effective for years to come.
If you are looking to improve the efficiency and longevity of your filtration system, consider the benefits of the Hydrodex FRP cartridge filter housing today.
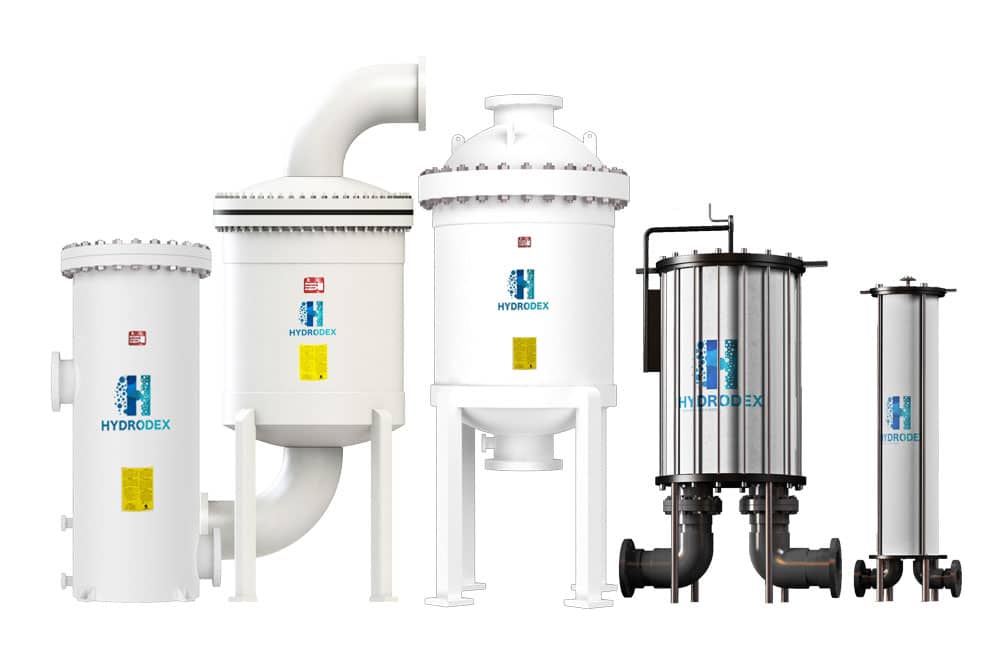
Hydrodex FRP filter housing
Reverse Osmosis RO Membrane Particle Fouling
Reverse Osmosis RO Membrane Particle Fouling is caused by organic and inorganic particles contained in the source seawater such as fine debris, plankton, detritus and silt, which cannot pass through the SWRO membranes. All suspended solids which naturally occur in insoluble form, if not removed by pretreatment, would be retained on the feed side of the Seawater Reverse Osmosis RO membrane. Depending on the hydrodynamic conditions on the membrane surface, as well as the size and charge of these particles, they would either migrate along the RO membrane leafs and ultimately exit with the concentrate, or would be trapped on the membrane surface and would begin to accumulate there causing loss of RO membrane productivity over time. This type of foulant can be effectively removed by pre-filtering of the source seawater prior to Seawater Reverse Osmosis RO membrane separation.
Reverse Osmosis RO Membrane Particle Fouling in raw source seawater vary in size. However, most of them, including pico-phytoplankton, are larger than 0.1 μm. Usually, over 90 % of the particulate foulants are larger than 1 μm. A well designed and operating pretreatment system will produce permeate that does not contain particles larger than 20 μm.
Reverse Osmosis RO Membrane Colloidal Fouling
Reverse Osmosis RO Membrane Colloidal fouling is caused by inorganic and organic compounds that naturally exist in suspension and may be concentrated by the SWRO desalination plant separation process, and precipitate on the Reverse Osmosis RO membrane surface thereby causing membrane flux decline over time. Colloidal solids have particle size of 0.001 to 1 μm. For prevention of Reverse Osmosis RO Membrane Colloidal Fouling, SWRO membrane manufacturers usually require RO membrane feed turbidity of less than 0.1 NTU, zeta potential higher than – 30 microvolts (mV) and SDI15 less than 3. The two most common culprits of this type of fouling are colloidal silica and iron.
Typically, seawater collected via open ocean intake does not contain significant amounts iron and silica in colloidal form and this type of fouling usually does not present a challenge in seawater desalination systems with open ocean intakes. Stability of colloids is reduced with the increase in source water salinity, and typical seawater with TDS concentration in a range of 30000 to 45000 mg/L, would contain silica and iron in dissolved and precipitated form rather than in colloidal form. However, if the source seawater is collected via subsurface well intake which is under the influence of brackish coastal aquifer with high content of colloidal silica and/or iron, or it is collected near an area where silt laden river enters into the ocean, than colloidal fouling may become a challenge. Reverse Osmosis RO Membrane Colloidal Fouling could be removed by coagulation, flocculation and filtration, which also applies to Reverse Osmosis RO Membrane particulate fouling.
Reverse Osmosis RO Membrane Mineral Scaling
Reverse Osmosis RO Membrane Mineral Scaling Causes: All minerals contained in the source seawater are concentrated during the process of membrane salt separation. As their concentration increases during the desalination process, ions of Calcium, Magnesium, Barium, Strontium, Sulfate and Carbonate can form sparingly insoluble salts which could precipitate on the membrane surface. The mineral scales that typically form during seawater desalination are these of Calcium Carbonate CaCO3, Calcium and Magnesium Sulfate (CaSO4 and MgSO4), and Barium and Strontium Sulfate (BaSO4 and SrSO4). Formation of mineral scales on the membrane surface is balanced by the high salinity of the seawater which tends to increase the solubility of all salts. This means that the higher the salinity of the source seawater the less likely a mineral scale forms on the membrane surface at typical seawater pH of 7.6 to 8.3 and desalination system recovery of 40% to 50 %. In brackish seawater desalination systems which typically operate at much higher recoveries (75% to 85%), and ionic strength of the source water is relatively lower, mineral scaling is a frequent problem. In typical seawater desalination systems, Reverse Osmosis RO Membrane Mineral Scaling is usually not a challenge, unless source seawater pH would need to be increased to 8.8 or above to enhance Boron removal.
Calcium Carbonate and Magnesium Hydroxide are the most common causes for Reverse Osmosis RO Membrane membrane scaling, when source seawater pH is increased for enhanced Boron removal. Scale formation in this case can be prevented by addition of antiscalant / dispersant to the source seawater. Commonly used parameters which can be used to predict the seawater’s potential to form mineral scaling of calcium carbonate are the Langelier Saturation Index (LSI) and the Stiff and Davis Index (SDI). These indexes are function of the source seawater pH, Calcium concentration, alkalinity, temperature and TDS concentration/ionic strength. It is important to note that although source seawater temperature usually has limited influence on scale formation, when this temperature exceeds 35°C, Calcium Carbonate scale would form at accelerated rate. Metal oxide and hydroxide foulants most frequently encountered during seawater desalination are iron, manganese, copper, zinc and aluminum.
Typically, open ocean seawater contains very low levels of these metal foulants and therefore, if such fouling is encountered on the membrane elements, the usual sources are overdosing of coagulant (iron salt) or corrosion of pipes, fittings, tanks and other metal equipment located upstream of the SWRO system / desalination plant. Iron and manganese fouling may occur if source seawater is collected via subsurface intake from a coastal aquifer which is under the influence of fresh groundwater that contains high levels of these metals in reduced form (iron of more than 2 mg/L (as ferrous) and manganese of more than 0.5 mg/L). This type of scaling problem has been observed in desalination plants with beach well intakes collecting seawater from alluvial coastal aquifers, which are located near the entrance of a river or a creek into the ocean.
If iron and manganese are in reduced form and they are below 1.0 mg/L and 0.1 mg/L respectively, than they can be removed by the SWRO membranes without causing accelerated fouling. However, if iron and manganese are in oxidized form, their levels should be reduced below 0.05 mg/Land 0.02 mg/L, respectively to prevent mineral fouling. Another mineral fouling compound frequently encountered in fresh surface water and brackish aquifers is silica. Open ocean seawater contains silica of less than 20 mg/L and therefore, this compound in not a typical cause of Seawater Reverser Osmosis RO membrane mineral fouling. Silica content above this level usually indicates that the source seawater quality is influenced by a fresh water discharge or coastal aquifer of high silica content located near the desalination plant intake area.
Reverse Osmosis RO Membrane Scaling and Fouling: Causes
Reverse Osmosis RO Membrane Scaling and Fouling have many reasons which will be discussed in this article. First, we need to learn the mechanism of desalination plants. In desalination plants, Seawater is collected from the ocean using either subsurface intakes (wells, intake galleries, etc.) or open ocean intakes. Subsurface intakes naturally pre-screen and pre-filter the collected seawater and thereby they remove coarse debris, and most of the sand and particulates from the seawater. Open ocean intakes which collect ambient seawater directly from the ocean typically have equipment (bar racks, fine traveling screens, micro-screens, and/or strainers) to pre-screen large debris, floating materials, large aquatic organisms, coarse sand, and stringy materials from the source water. As a result, after preliminary screening by the intake facilities seawater typically contains the following five key groups of compounds that could cause Seawater Reverse Osmosis RO membrane scaling and fouling and therefore, would need to be removed by the pretreatment system:
- Particulate foulants (Mainly suspended solids and silt).
- Colloidal foulants: Compounds of relatively small size (0.2 μm to 1.0 μm) that are not in fully dissolved form. When concentrated during the membrane separation process they may coalesce and precipitate on the membrane surface (mainly clay-like substances).
- Mineral scaling foulants: Inorganic compounds (i.e., Ca, Mg, Ba, Sr salts) which during the salt separation process may precipitate and form a scale on the membrane surface (such as Calcium Carbonate CaCO3 and Calcium Sulfate CaSO4, and magnesium hydroxide) or may block the membrane diffusion layer (such as Iron and Manganese).
- Natural organic foulants: Natural organic matter that can attach to and foul the membranes.
- Microbial foulants: Marine organisms and soluble organic compounds that can serve as food to the microorganisms which inhabit in the source water and can form fouling biofilm reducing membrane transport.
Please visit the Hydrodex BLOG to learn more about each key group of compounds and how to prevent your RO membrane from scaling and fouling.